Much of the current and upcoming stage in Rosslyn’s icehouse rehab involves covering, cladding, and closing in: clapboard siding, T&G nickel gap paneling, upcycled garapa paneling, and plenty of hardwood flooring. Today I’d like to get you up-to-date on the loft flooring.
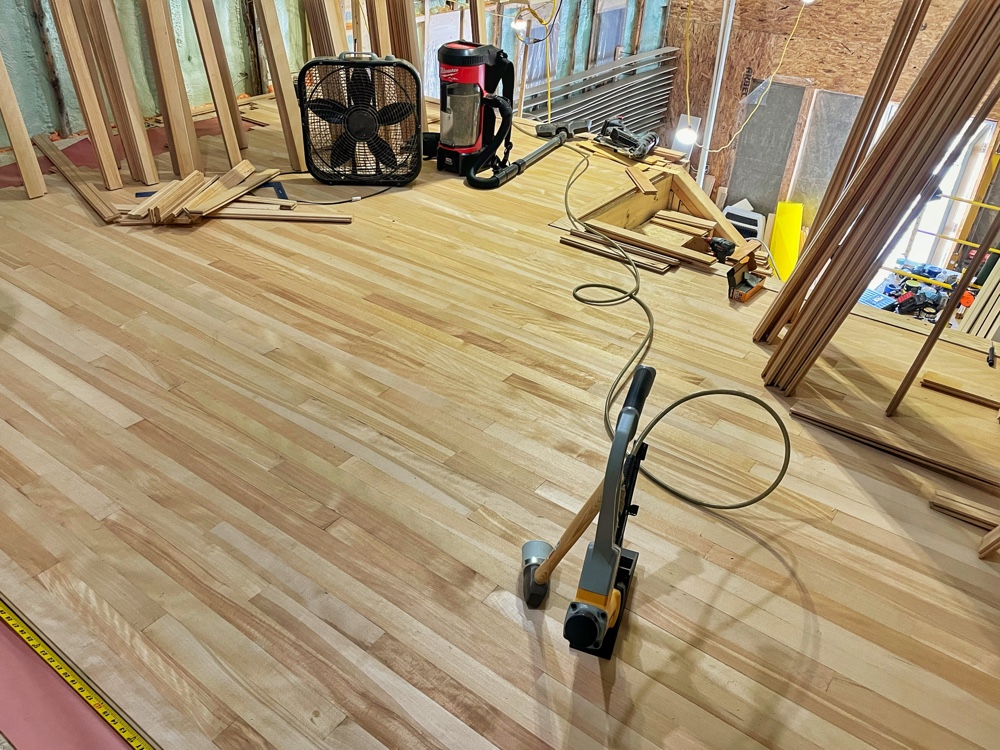
We’ve installed beech flooring that remained from the first floor reflooring (entrance hallway, living room, parlor, and kitchen) completed in 2007-8. Stored in the icehouse for the last decade and a half with plenty of additional surplus building materials, this handsome hardwood — originally selected for its local origins, pale color, and character-rich grain — has been repurposed as our new loft flooring.
But, as often, I’m getting in front of myself. Before installation came acclimatization…
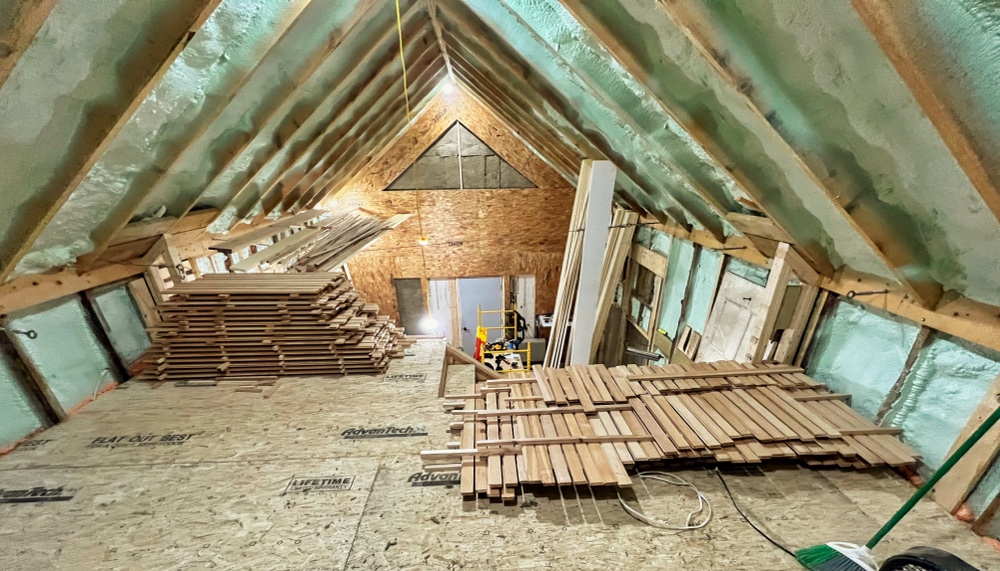
Acclimating Beech Flooring
A few weeks ago Tony and Peter relocated the beech hardwood flooring from one of the storage containers to the icehouse loft area where it was stacked and stickered strategically to maximize through-flow of warm, dry air. Frequent metering enabled us to track the moisture content of the flooring as it stabilized.
Within a couple of weeks the temporary improvements to temperature and humidity control in the icehouse implemented Peter and Eric proved their value. The beech was ready to be installed.
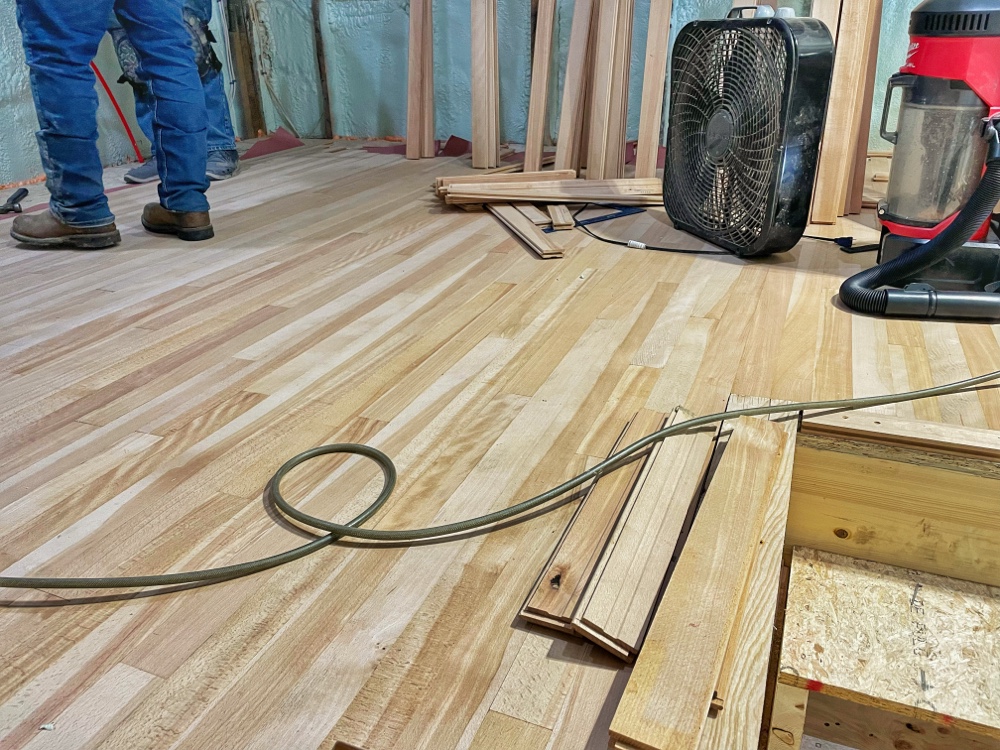
Loft Flooring Installation
The beech was oriented perpendicular to the loft floor joists, starting at the east edge of the loft where we temporarily attached spacers (retainers for railing bottoms and the top stairway tread) to accurately determine the flooring’s start point. Beginning on this side enabled us to minimize the likelihood of a visible “pie wedge” given less than perfect geometry of our 130+ year old building.
Prior to working west from the loft overhang, yes team marked out locations for future cabinets that will be fabricated and installed along the north and south knee walls. Because we were using remnant flooring (think limited quantity) we needed to prioritize the area of the floor that would be visible once the cabinetry was in place. We ran the flooring “ragged” under the cabinets — underlaying the figure cabinets without extending all of the way to the wall, allowing us to ensure sufficient material for the exposed area of the floor.
Especial attention was paid to sequencing beech boards in a visually attractive progression, board-to-board, ensuring that the color and character variations would enhance the cohesive integration across entire floor.
Another less visible but important detail: integrating the top stair tread. Peter shaped a beech slab to frame the flooring at the top of the staircase, routering in a tongue for the 90° conjunction between flooring and beech stair tread. This has added a little extra time, but it ensures a more stable joint in a high traffic, high visibility transition.
Now that the loft flooring is installed, it’s time for sanding and sealing. I’ll post an update soon!
Leave a Reply